Die Finite-Elemente-Simulationssoftware für Konstrukteure
Große Baugruppen einfach simulieren.
Entwickelt für den Maschinenbau.
Entwickelt für den Maschinenbau.
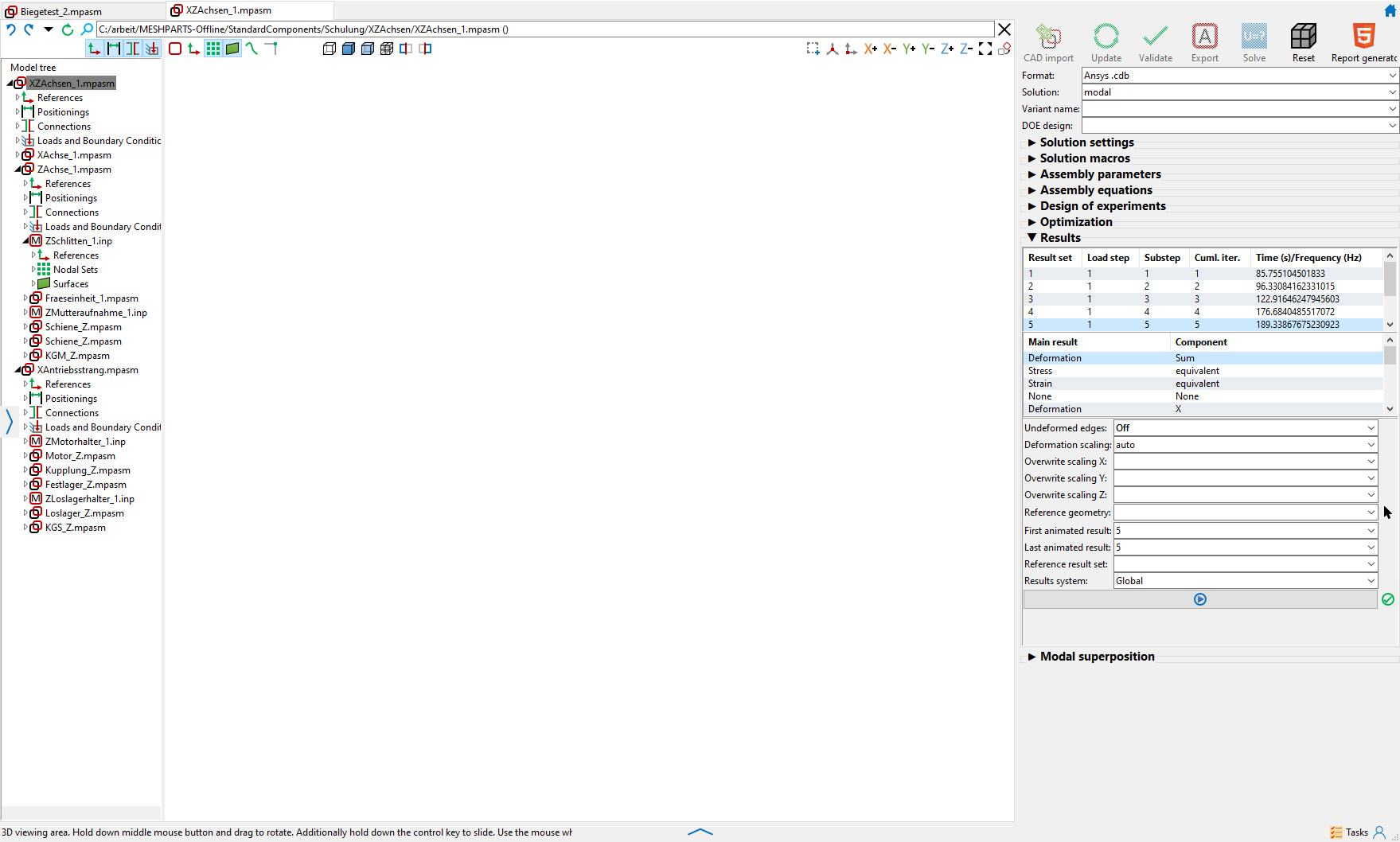
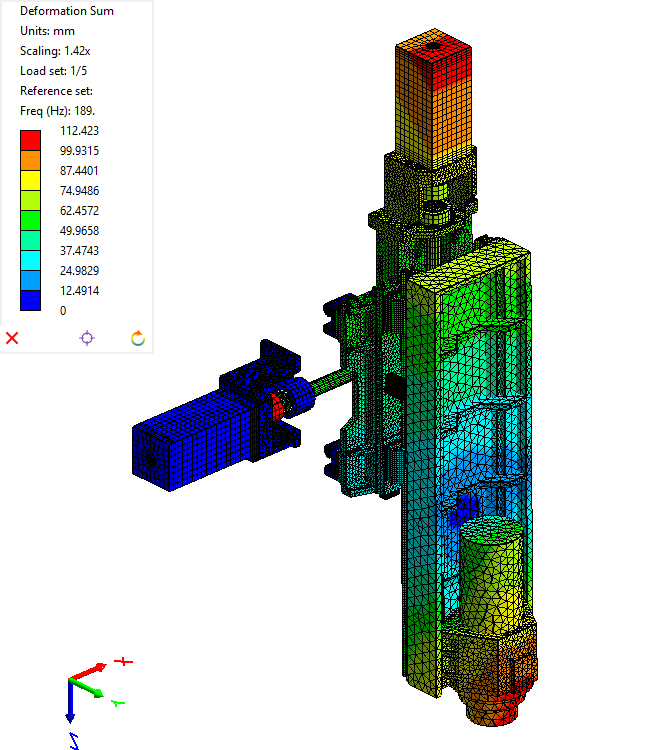
Kunden
Branchenführende Unternehmen vertrauen auf Meshparts
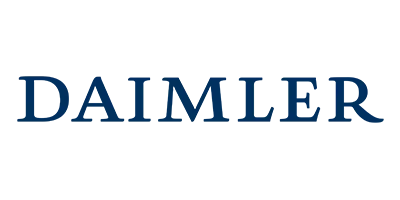
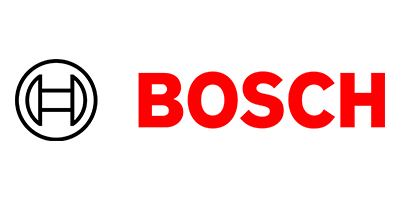
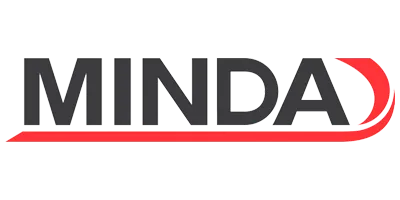
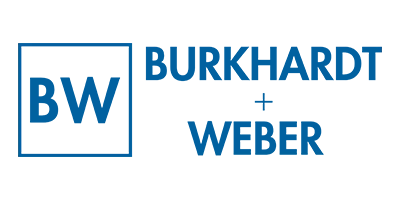
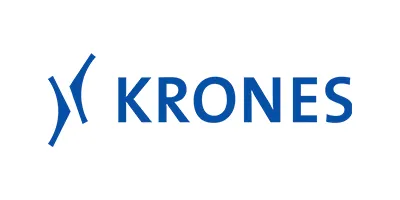
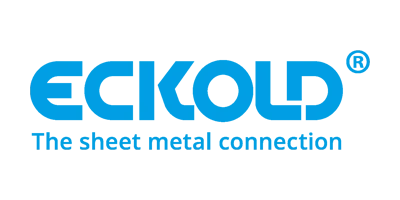
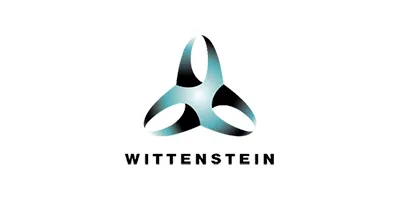
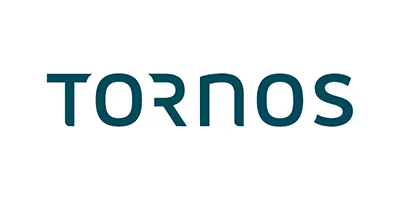
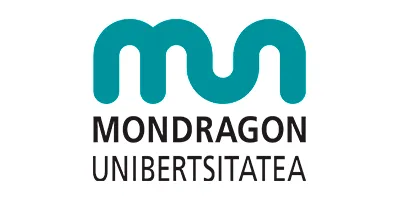
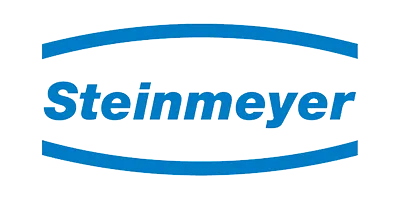
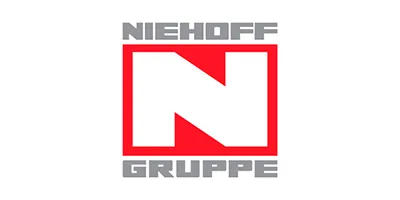
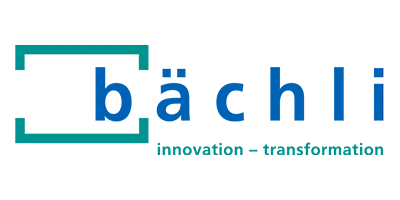
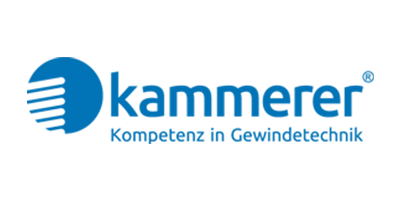
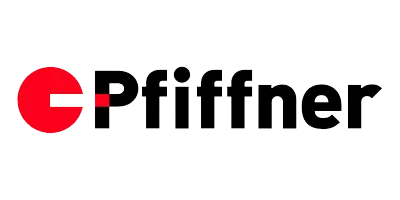
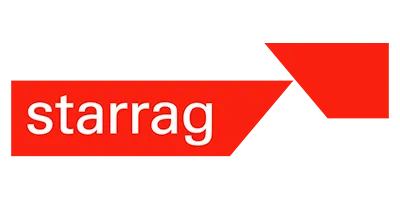
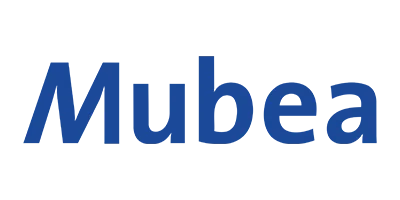
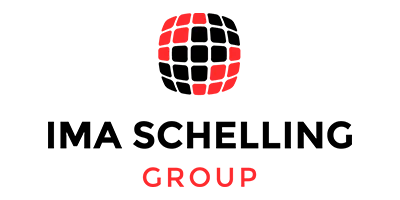
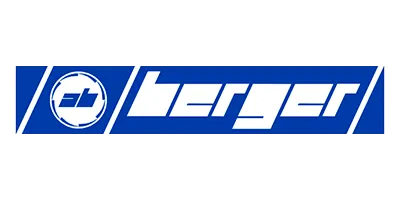
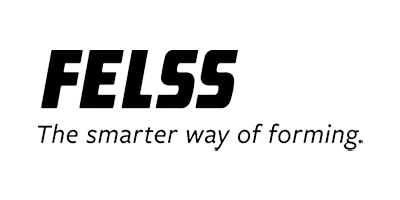
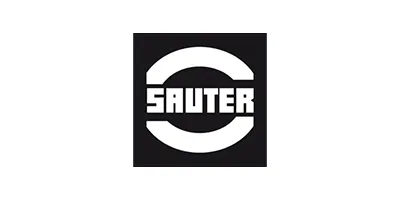
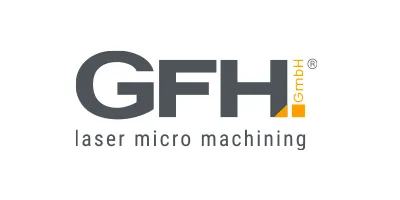
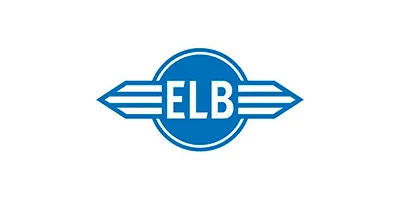
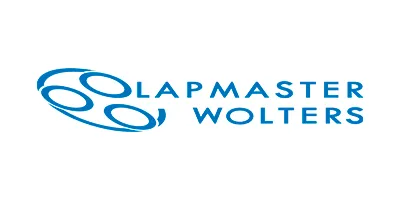
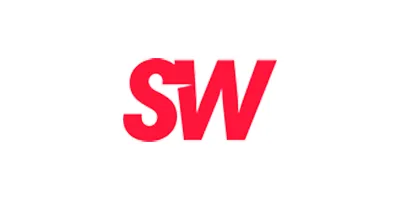
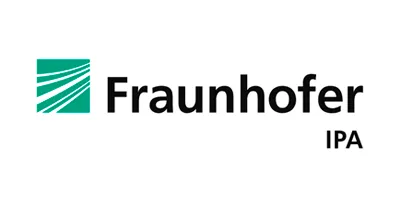
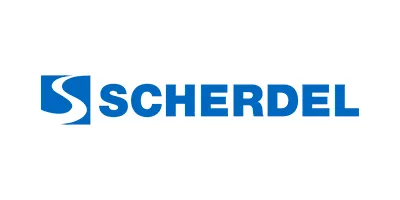
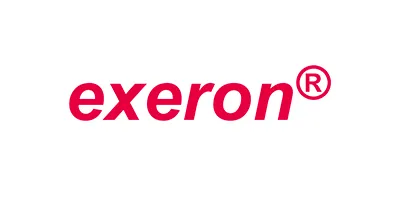
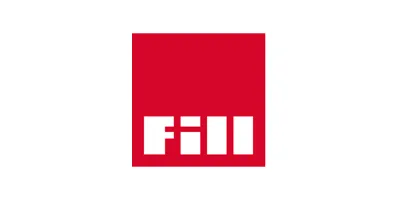
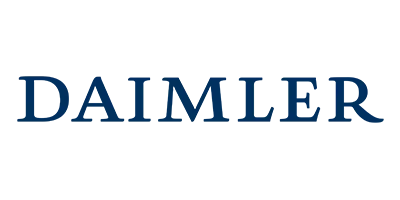
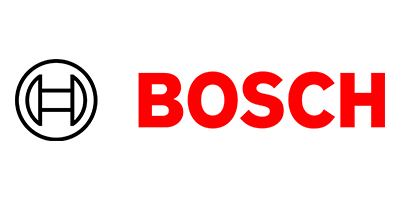
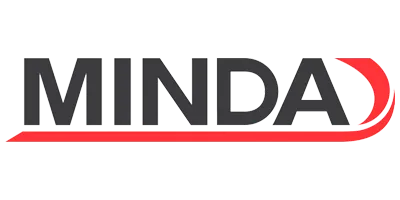
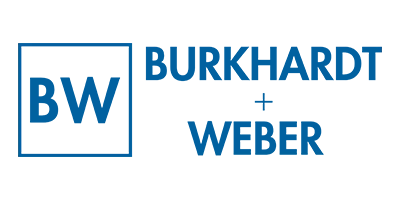
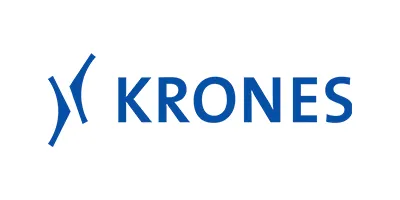
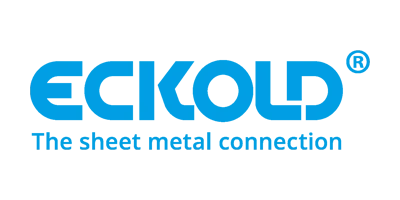
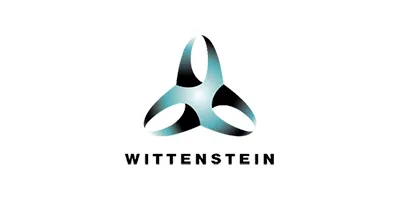
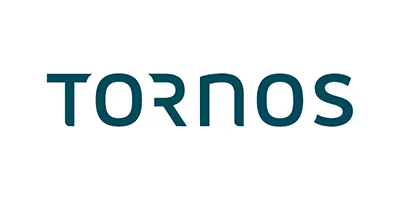
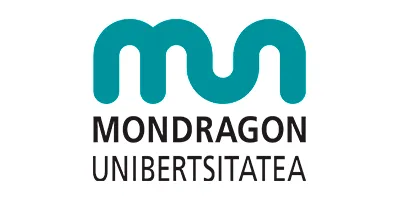
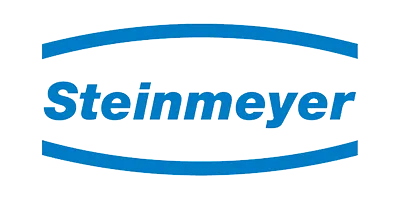
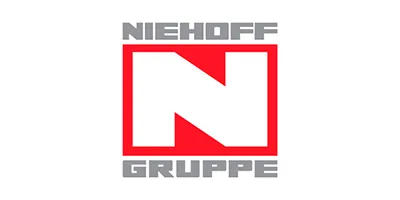
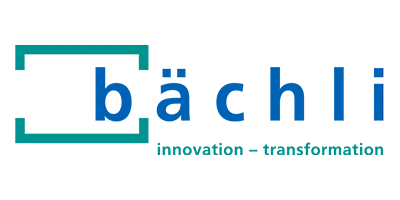
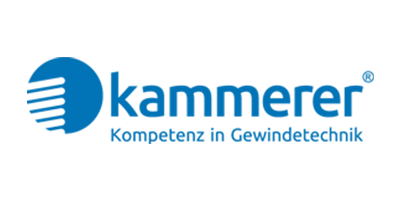
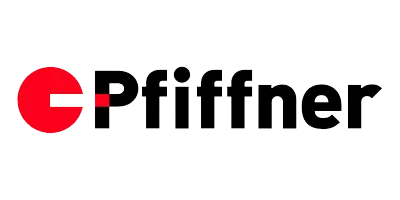
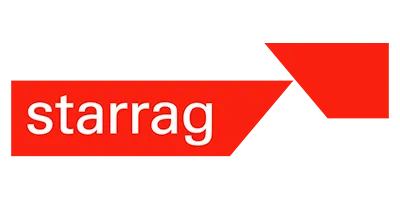
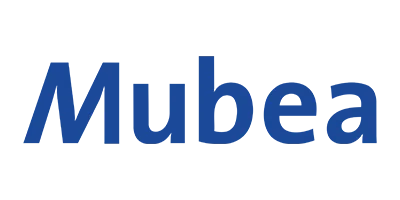
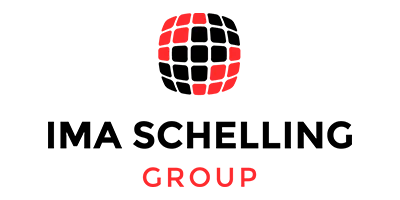
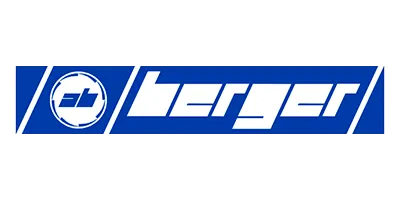
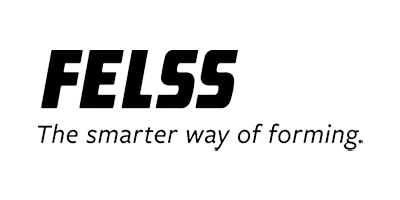
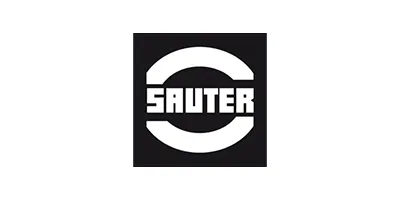
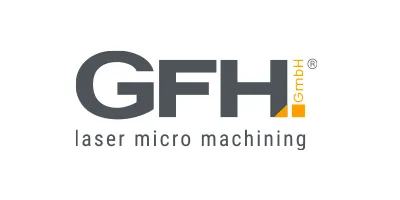
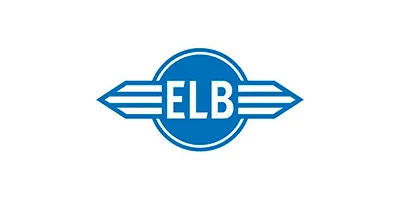
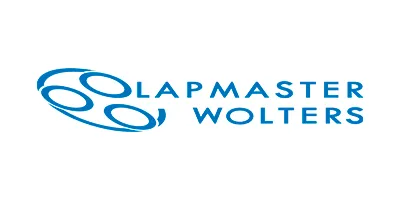
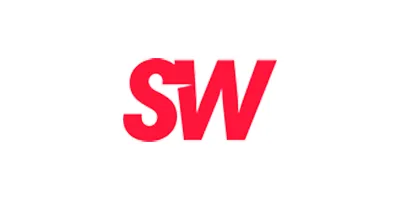
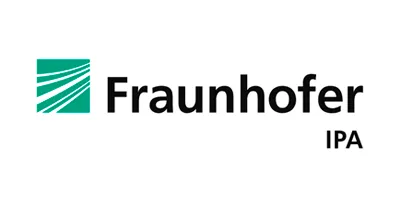
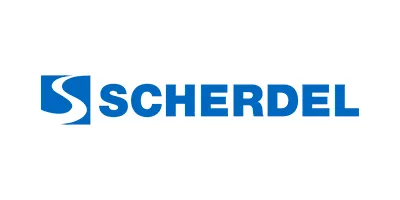
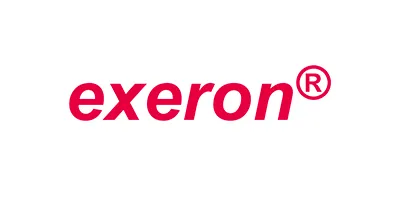
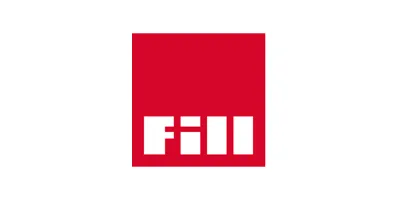
Funktionen
Mit einem Tag Schulung auf Expertenniveau simulieren
Messgenaue Ergebnisse
In zahlreichen Kundenprojekten wurden die mit Meshparts erzeugten Simulationsergebnisse mit Messungen verglichen. Abweichungen von weniger als 5% sind nicht selten erreichbar
Intelligente Assistenzsysteme
Meshparts unterstützt den Anwender bei den typischen FE-Herausforderungen wie Netzerstellung, Kontaktfindung, Definiton von Randbedingungen
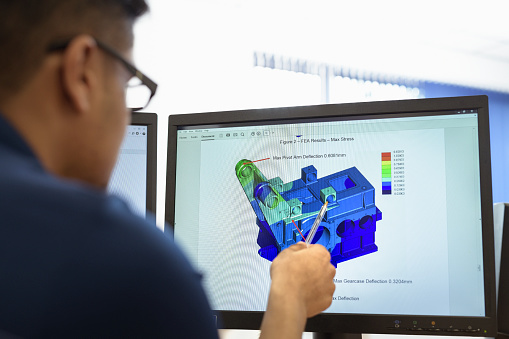
Struktur-Mechanik
Komprimiertes Spezialwissen für den Maschinenbau wie Dauerfestigkeitsnachweise auf Knopfdruck
Mehr Details ansehen
Live Support
Kein Warten in der Warteschleife und keine Tickets mit mehreren Tagen Bearbeitungszeit. Nehmen Sie per Videokonferenz Kontakt zu einem unserer Ingenieure auf
Mehr Details ansehen
Struktur-Dynamik
Identifikation von gefährlichen Resonanzstellen und Ermittlung von Schwingungsamplitunden an ausgewählten Stellen
Mehr Details ansehen
Automatische Zukaufteile
Durch die Part-Mappings ist die Meshparts-Software lernfähig. Sie werden mit jedem neuen Modell immer schneller in der Modellierung von FE-Baugruppen
Mehr Details ansehen
Finite-Elemente-Modellbibliothek
Nutzen Sie eine umfassende Bibliothek mit über 60.000 präzisen Komponentenmodellen der meistgenutzten Zukaufteile im Maschinenbau.
Ganz ohne Modellierungsaufwand, Modellierungsfehler, Expertenwissen
Ganz ohne Modellierungsaufwand, Modellierungsfehler, Expertenwissen
Integrationen
Nutzen Sie mehrere Integrationen wie den CAD Twin, um Ihr Produkt zwischen CAD und Meshparts zu synchronisieren oder nutzen Sie unsere PDM-Integration.
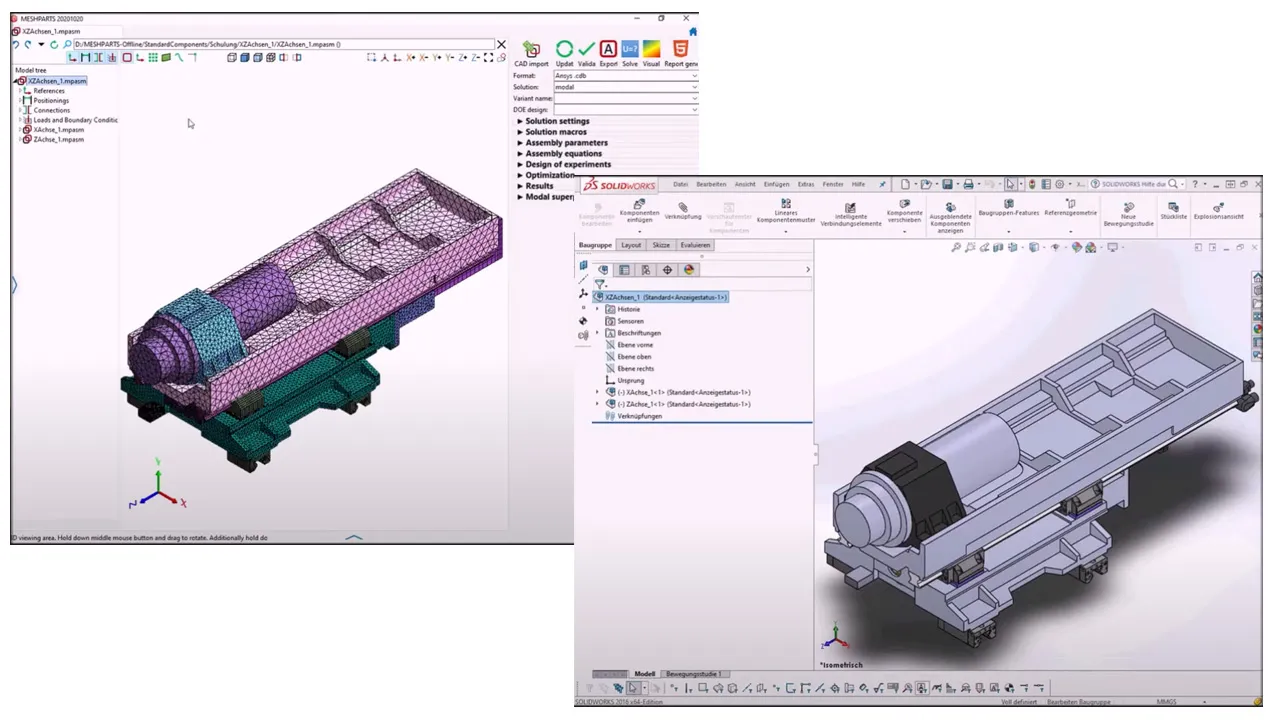
Erfolgsgeschichten
Erfolgsgeschichten unserer Kunden
Kundenstimmen
Bewertungen unserer Kunden
"Sehr schnelle Projektbearbeitung mit umfassender Beratung aufgrund hoher Projektkomplexität"
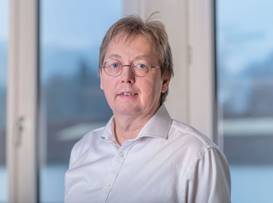
Frank Hanisch
Technischer Leiter, Forschung & Entwicklung bei Bächli AG
"Meshparts ist ein modernes und sehr durchdachtes FEA-Programm, das uns ermöglicht, komplexe Baugruppen-Simulationen im Bereich des Sondermaschinenbaus mit hoher Modellierungsqualität und einem zugleich vertretbaren Zeitaufwand durchzuführen. Aus meiner Praxis mit Meshparts heraus schätze ich das übersichtliche und CAD-ähnliche Bedienkonzept. Zu guter Letzt: Ein großer Pluspunkt von Meshparts ist der zuverlässig erreichbare und sehr kompetente Support."
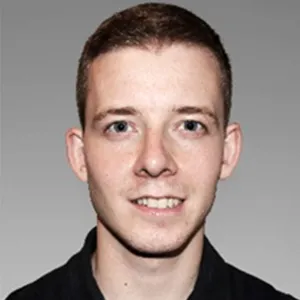
Chris Hopmann
Leiter Analysen & Berechnungen bei IMA Schelling Group
"Meshparts gibt uns da die Möglichkeit auch größere Baugruppen mit vielen Schrauben und Kontaktbedingungen, mit einem vertretbaren Aufwand als FEM-Modell zu definieren und umfassend mehrere Lastfälle zu analysieren. Das spart unnötige Konstruktionsschleifen und Kosten."
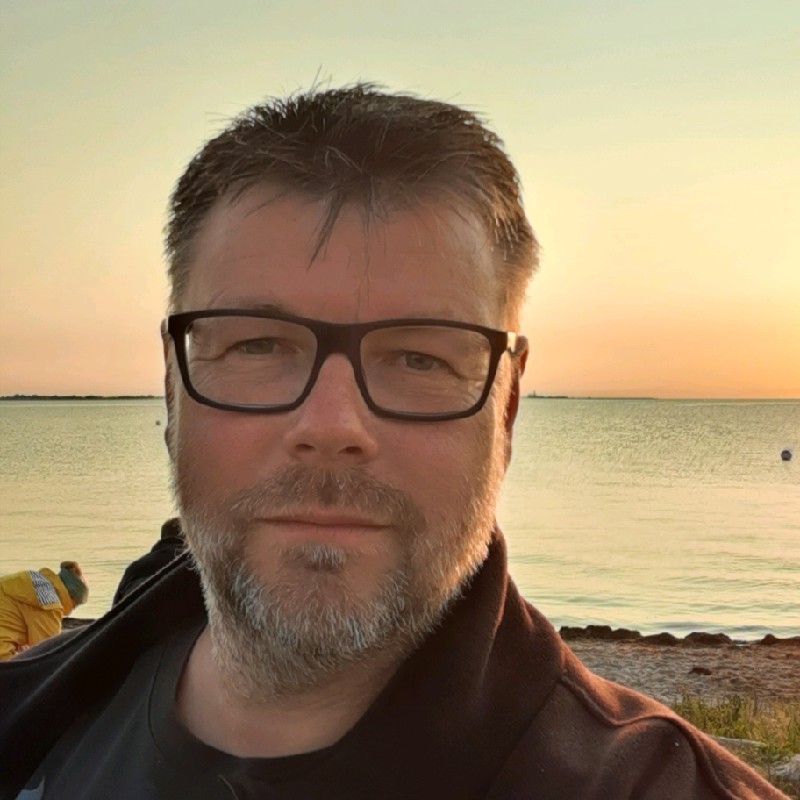
Bernd Polossek
Leiter Konstruktion und Design bei ECKOLD GmbH & Co. KG
"Das Verständnis für die Anforderungen des Marktes, das tiefe Fachwissen im Bereich Maschinenbau und Simulation, sowie die Geschwindigkeit des Supports sind beeindruckend und stellen einen Benchmark dar."
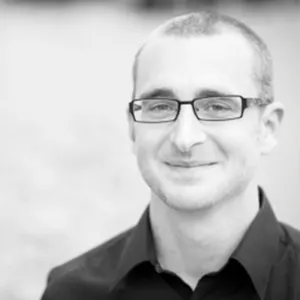
Jörg Common
Leiter Entwicklung bei Felss Systems GmbH
"Bei der Auslegung eines neuen, dynamisch stark belasteten Kugelgewindetriebs mit Doppelmutter wollten wir eine gegenüber der Normberechnung höhere Sicherheit erreichen. Meshparts hat dabei mit den notwendigen Simulationsuntersuchungen unterstützt. Dank der extrem detaillierten FE-Modelle, konnten wir problemlos auch die lastabhängige Kontaktwinkeländerung für jede einzelne Kugel im Modell auswerten."
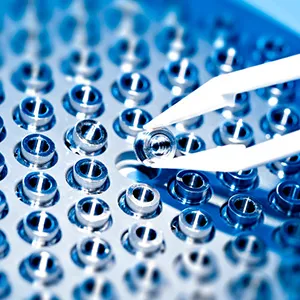
Maximilian Hiemer
Konstruktionsleiter bei A. Berger GmbH & Co. Präzisions Maschinenbauteile KG
"Eine kurzfristige und schnelle Bearbeitung mit fundiertem Fachwissen im Werkzeugmaschinenbereich"
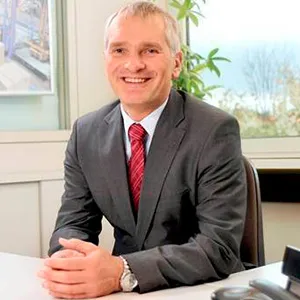
Dr. Hubertus Zeddies
Technischer Leiter bei Minda Industrieanlagen GmbH
Webinare
Aufgezeichnete Meshparts Webinare
"Kurzfristige und schnelle Bearbeitung, fundiertes Fachwissen im Werkzeugmaschinenbereich"
Dr. Hubertus Zeddies
Technical Management, Minda Industrieanlagen GmbH
Anwendungsfälle
Anwendungsfälle von Finite-Elemente-Simulationen
Kostenlose Potentialanalyse anfordern
Entdecken Sie in einer kostenlosen Potentialanalyse mit einem unserer Experten, welchen Mehrwert Meshparts Ihrem Unternehmen bieten kann.
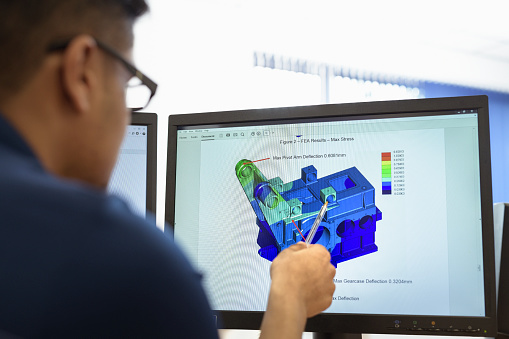