Glossar
Erfahren Sie alles rund um das Thema Finite Elemente und dessen eindrucksvolle und kostensparende Simulationen.
Kostenlose Potentialanalyse anfordern
Entdecken Sie in einer kostenlosen Potentialanalyse mit einem unserer Experten, welchen Mehrwert Meshparts Ihrem Unternehmen bieten kann.
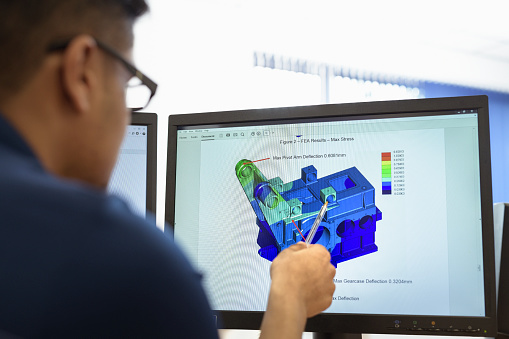