Der Kugelgewindetrieb - Das Antriebselement
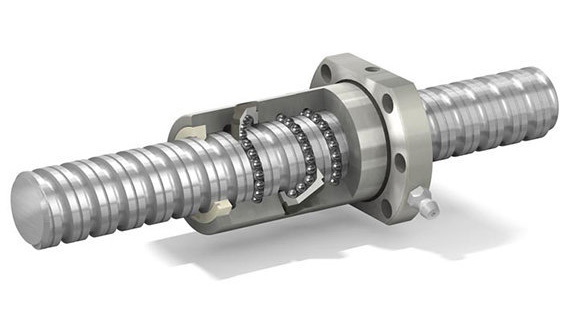
Kugelgewindetriebe zählen zu den meist eingesetzten Antriebselementen. Mit der voranschreitenden Elektrifizierung von Produkten erschließen sie zudem neue Anwendungsbereiche, in denen bisher meist Hydrauliksysteme Verwendung fanden. Prominente Beispiele sind hier die Aktorik für Pressen und Servolenkungen sowie Flugzeuglandeklappen und Hubschrauberrotoren.
Aufgrund der neuen Einsatzbereiche ergeben sich neue Belastungsarten und somit immer größere Anforderungen an die präzisen Drehmoment-Kraftumwandler. Wenn Kugelgewindetriebe früher rein axiale Kräfte aufnehmen mussten, so müssen diese heute teilweise große radiale Kräfte sowie Kippmomente aufnehmen. Die Belastungen gehen teilweise über die Streckgrenze des Materials hinaus.
Die klassischen Auslegungsmethoden wie bspw. die DIN-Norm reichen nicht mehr aus, denn diese gehen von einer gleichmäßigen Kräfteverteilung auf die einzelnen Kugeln aus und setzen großzügige Sicherheitsfaktoren voraus.
Wer heute Zeit und Kosten bei der Auslegung von hochbelasteten Kugelgewindetrieben sparen und gleichzeitig qualitativ hochwertige Ergebnisse für seine Kunden erzielen soll, setzt auf die Simulation von Kugelgewindetrieben.
Simulation von Kugelgewindetrieben
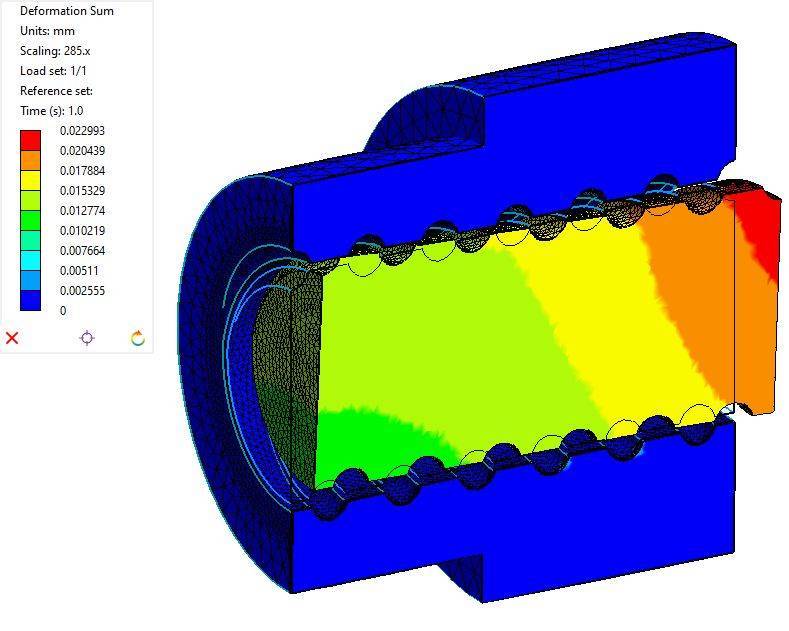
Richtig eingesetzt, ermöglicht die Simulation von Kugelgewindetrieben eine optimale Auslegung mit sehr geringen Sicherheitsfaktoren. Das wird typischerweise von der Flugzeugindustrie aus Gewichtseinsparungsgründen verlangt. Durch die präzise Berechnung von Kugelkräften und -pressungen können Lebensdauerberechnungen zuverlässiger durchgeführt werden. Auch kombinierte Lastfälle sind kein Problem – etwas, was sonst bei der DIN-basierten Auslegung nur stark eingeschränkt möglich ist. In den meisten Fällen kann die Simulation Prüfstände, Prototypen und Tests ersetzen. Ferner kann in der Simulation der Einfluss der umgebenden Konstruktion (Mutterbock, Wälzlagerung der Spindel usw.) berücksichtigt werden. Das computerunterstützte Engineering von Kugelgewindetrieben ermöglicht schließlich automatisierte Parameterstudien, um das beste Design aus einer Fülle von Möglichkeiten auszuwählen. Die Krönung der Kugelgewindetrieb-Simulation betrifft die adaptive Optimierung der Kugelvorspannung. Das Ziel der adaptiven Kugelvorspannung besteht darin, die Geometrie der Kugellaufbahn oder der Kugeln in den einzelnen Kugelketten entsprechend der Belastung so anzupassen, dass alle sich in Kontakt befindenden Kugeln eine möglichst gleiche Last aufnehmen.
Pioneer-Arbeit in der Simulation von Kugelgewindetrieben
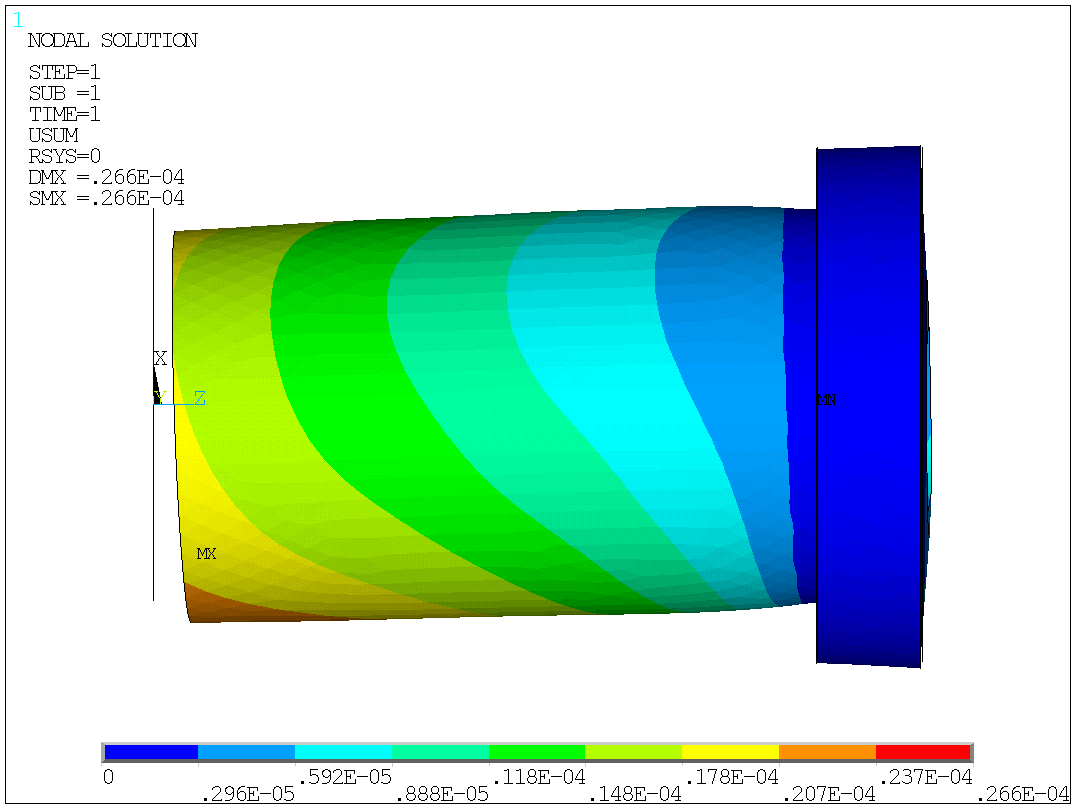
Wir von Meshparts verfügen über einen großen Erfahrungsschatz über das Verhalten von Kugelgewindetrieben sowie über die modernsten Methoden zur effizienten Simulation von Kugelgewindetrieben. Der Bereich "Simulation Kugelgewindetriebe" wird bei uns im forschungsnahen Umfeld seit 2011 entwickelt und baut auf Vorarbeiten auf, die noch einige Jahre davor entwickelt worden sind. Seitdem betreiben wir kontinuierliche Pionierarbeit, um die Simulation von Kugelgewindetrieben mit maximaler Effizienz durchführen zu können. Maximale Effizienz bedeutet große Ergebnisgenauigkeit bei kleinstem Aufwand. Dieser Anspruch betrifft die Modellierung von Kugelgewindetrieben, deren Berechnung sowie Ergebnisauswertung.
Im Laufe der Zeit gab es viele Momente, wo wir dachten, dass wir die Entwicklung für die Simulation von Kugelgewindetrieben finalisiert hätten. Kurze Zeit darauf ergaben sich dann im Rahmen von Kundenprojekten und praxisnahen Anwendungsfällen neue Ideen, die dann unsere Produkte über alle bisherig geltenden Effizienzgrenzen katapultiert hatten. Wir wundern uns immer wieder, was alles noch möglich ist. Wir wissen mittlerweile, dass die Entwicklung nie zu Ende ist. Das Ganze tun wir aus einer inneren Antriebskraft, aus der Überzeugung, dass der Hersteller von Kugelgewindetrieben eine Simulationslösung braucht, die aus der Praxis für die Praxis erschaffen ist. Wir wissen einfach, dass gute Software und Dienstleistungen nicht teuer sein müssen, wenn die Prozesse optimiert und spezialisiert sind.
Zwei Lösungen für die Simulation von Kugelgewindetrieben
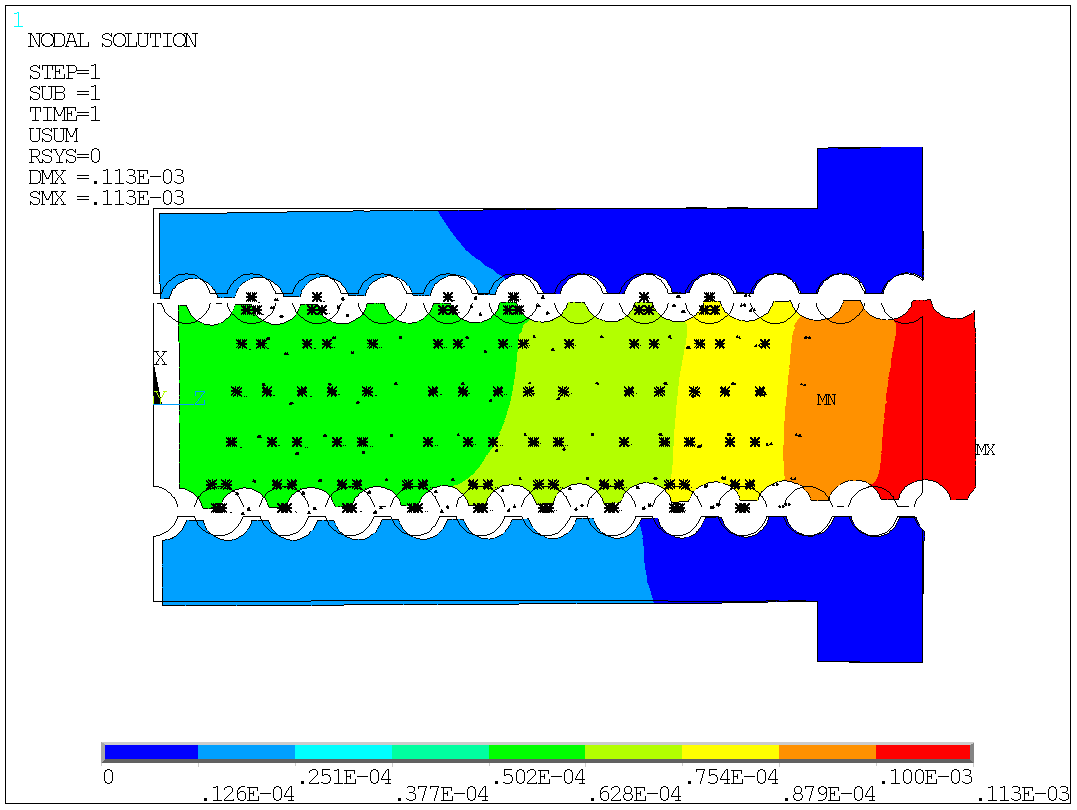
Was können wir Ihnen anbieten, damit Sie Ihre Kugelgewindetriebe simulieren und optimieren können? Unser Angebot gliedert sich wie folgt:
- Falls Sie selten eine Simulation brauchen, dann empfehlen wir unsere Dienstleistungen.
- Falls Sie gelegentlich bis oft simulieren möchten, dann empfehlen wir unserere Software im Zusammenhang mit der Modellbibliothek für Kugelgewindetriebe.
Software für die Simulation von Kugelgewindetrieben

Unsere Software im Zusammenhang mit der Modellbibliothek für Kugelgewindetriebe wird lokal installiert. Sie haben die Möglichkeit beliebig viele Designvarianten von Kugelgewindetrieben zu berechnen. Die Software ist als Jahres- oder Monatsabo zu haben. Wir leisten auf Wahl Standardsupport (max. 8 Stunden pro Jahr) oder intensive Wartung- und Support (8 Stunden pro Monat). Dazu empfehlen wir noch eine eintägige Schulung.